
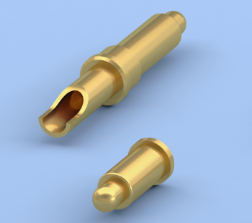
Variety of loose pogo pins and pogo pins in 3-pin assembly holders and with Pick and Place caps.
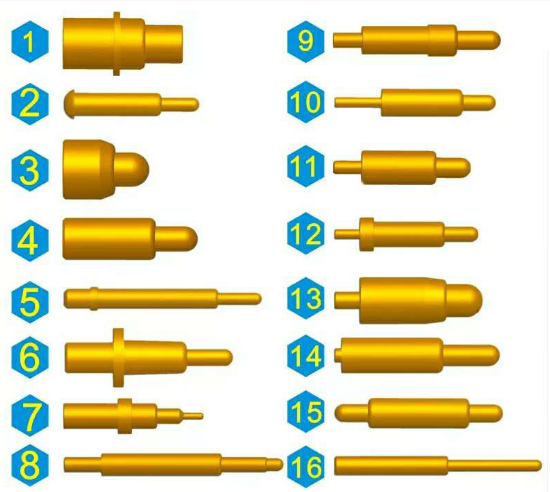
OMRON’s blade pins help customers reduce maintenance man-hours and improve production efficiency.Pogo pin. The mechanical durability of OMRON’s testing pins is over 500,000 times, approximately five times more than that of pogo pins. Therefore, if the pin durability is low, 100 to 10,000 pins on the inspection equipment must be replaced daily, depending on the inspection requirements of the device under test (DUT). The number of times semiconductor components that are part of our daily lives are inspected ranges from tens of thousands to hundreds of thousands of times per day. *An example of B-to-B connector inspection Four Values Provided by the Blade Pinīecause the testing pin used for the inspection of small components such as semiconductors is very thin, with a diameter of 1 mm or less, durability is an issue. High inspection accuracy even for devices under test that require low contact resistanceĭifficult to use for devices under test that require low contact resistance Pogo Pin and OMRON’s Probe Pin (Blade Pin) What is Pogo Pin? *Two patents (US8337261 US2013/0045617) have been granted for the electroforming technology to form the contact structure and its manufacturing process. In addition, OMRON’s plate-shaped probe pins excel at pin placement with narrow pitch spacing for the inspection of high-performance, high-density products.Ĭontact OMRON with your concerns and consultation regarding the inspection of extremely small electronic components. OMRON’s testing sockets boasting high durability (long operating life) and high precision contribute greatly to the reduction of maintenance man-hours for customers. With our EFC process technology and many years of know-how, we propose sockets with a shape suitable for the customer’s device under test (DUT) with the same design speed as that of pogo pin products while achieving better inspection characteristics than pogo pin products. Highly durable pins with complex shapes and excellent spring property that are difficult to fabricate by metal bending or other processing can be manufactured with precision on the order of microns. OMRON’s testing sockets use probe pins manufactured using its proprietary* electro formed components (EFC) process technology. Inspection equipment for electronic components requires not only technical capabilities to respond to the speed, but also high measurement accuracy to accurately check the performance of extremely small electronic components and a narrow pitch to accommodate increasingly high-density products. Applications that support social infrastructure such as smartphones have a fast release cycle for new products, so the socket shape on the inspection side changes each time. Naturally, there are various shapes of sockets used in the inspection equipment for these components. Ultra-compact electronic components are now used in various applications that support the foundation of our lives, such as smartphones, car navigation systems, and advanced driving technology. OMRON’s EFC Process Technology (Electroforming Microfabrication Technology).
